
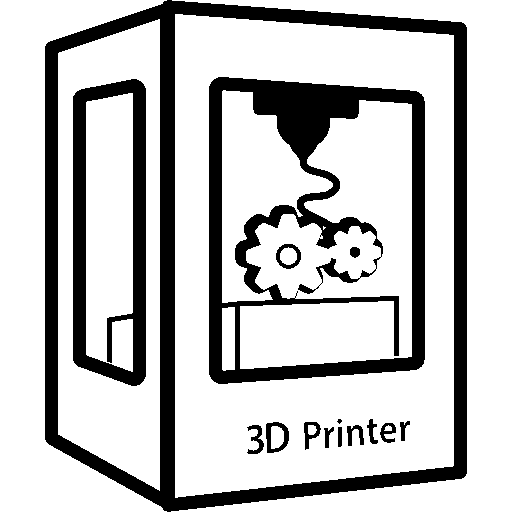
Bad bearing on a moving part. Or a bur along a rail, It catches just enough to cause the smooth motion to jitter a bit as the head moves along. Blobbing the material down instead of spreading it nice and even.
Bad bearing on a moving part. Or a bur along a rail, It catches just enough to cause the smooth motion to jitter a bit as the head moves along. Blobbing the material down instead of spreading it nice and even.
You have a draft going through your room, I used to have same issue when my printer was beside a window. Less when I moved the printer to middle of the room and issue was gone when put the printer into a closet. With closed doors.
You can try lowering bed temperature to, the warm bed keeps lower layer pliable but the upper layers cool and contract pulling the more flexible layer up and away. So a cooler bed temp should make the bottom layers more ridgid.
Everyone worried about the bending force, the retaining slots will tear out and drop the damn thing on the desk well before it bends.
Now do it like 5 or 6 more times on the rest of the bed and now it’s textured for extra adhesion.
Can you post the g code ?
What printer do you use. This is a mechanical issue. It’s something binding as the one x or y is traveling could be a bearing or the stepper motor it self. It prevents the arc from being fully formed even though the machine thinks it is key point you made is that randomized z seam leaves the same mess, but if notice it’s not all the layers are cut short only some.
Take the belt off and move the axis by hand slow and easy do you feel anything that isn’t smooth like silk? That would be it. Feel the stepper is the drive gear tight any slip ?? Any play in the shaft side?
Edit
Looking at the pictures again I’d bet that if you went taller and printed faster, it would be even worse because the bad part got hotter and more bound up more Alternatively printing faster might make it better because you have the inertia to push past the binding spot.
Ig you think that’s bad wait until you get multiple retractions going that the rocking motion of the 3kg Is probably going to be enough to pull the filament right out of the extruder.
120grit sand paper give it a scuff and rubing alcohol before each print. That solved almost all of my issues with bed adhesion and let me get away with it where normally it would fail. Anything else it’s probably out of level bed or actual frame of the machine has a bend or low spot. If your z offset was bad you would have that happening all over the the first layer. If you have a bl touch on your set up, make a grid amd write down each number if there is a difference in the corners it’s bed level If it’s middles / sides it’s a low spot in frame some materials tolerate out of level better then others.
I’ve been using a 1/4" thick sheet of carbon fiber for years now. Once warmed up to temp prints stick hard on it. As soon as it’s cool a breeze can push a print of the bed. Plus it won’t shatter like glass does eventually, boy was that a surprise. You still have to wipe clean with some rubbing alcohol before printing.