
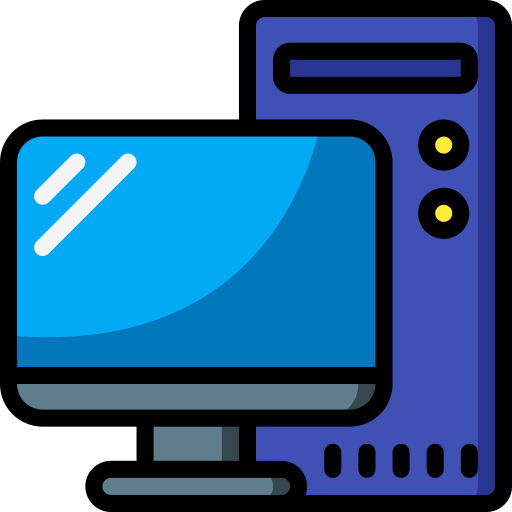
I run some of my services (until very recently including jellyfin) on my HP pavilion G6 from 2007. It still runs my wireguard, backup pihole, heimdall, etc. I run it on Linux mint (it was familiar) and cant do most things on screen (lags hard) but I can ssh or VNC in just fine
I torrented and seeded many torrents (its still seeding right now) and it can do at least 2 (havent tried more) jellyfin streams at once as long as I disable server side transcoding to reserve resources. I had the full arr suite of apps running along with ombi (gonna move to jellyseer, but imo ombi used too much ram on my 4GB laptop to be something I kept running). Is it perfect? No, it has quirks that will come up now and again but can I really complain when getting now 16 years of use out of a laptop I never thought I’d touch again once I built my desktop?
Edit: oh be aware, if you’re using old hardware, DO NOT use the newest versions of things like Linux mint, it possibly won’t have drivers that works for really old hardware (like wifi card, Lan card, etc.) and it won’t be easily apparent sometimes. I solved this with a friend who had the same laptop as me but couldn’t get internet once installing mint. It turns out he used a newer version of mint that did not have a way to support his wifi card and installing and older version solved it